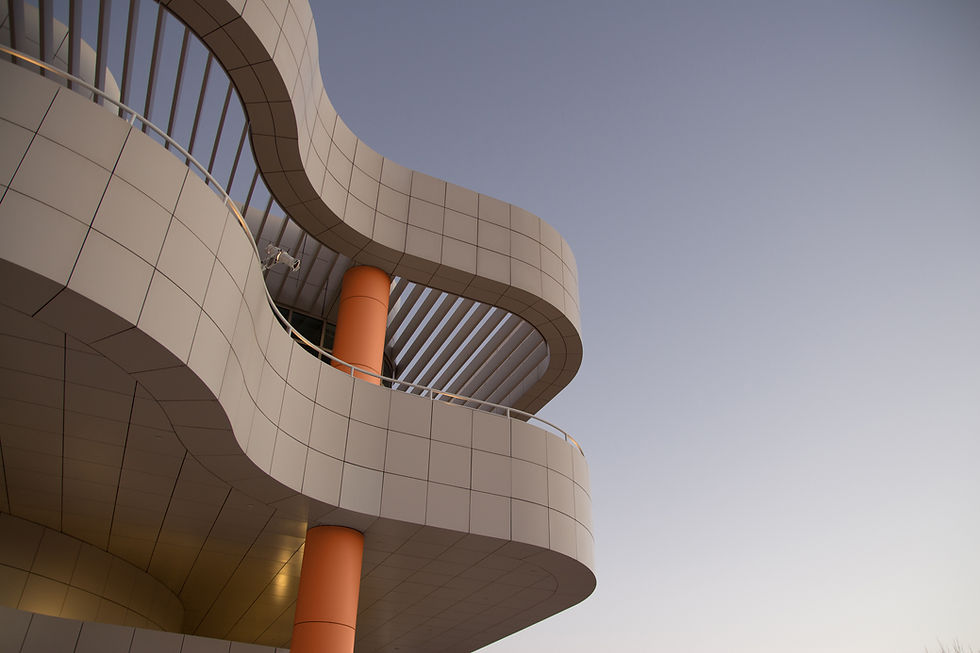
TL;DR
Y = f(x) represents the relationship where outputs (Y) are determined by inputs (x) in a process.
In Six Sigma, this equation helps identify critical factors affecting process outcomes.
It's integral to the DMAIC (Define, Measure, Analyze, Improve, Control) methodology.
By analyzing Y = f(x), organizations can pinpoint and optimize key inputs to enhance quality.
Real-world applications span manufacturing, services, and healthcare sectors.
Introduction
In Six Sigma, understanding the factors that influence process outcomes is crucial. The equation Y = f(x) serves as a foundational concept, illustrating that the output (Y) is a function of various inputs (x). This relationship underscores the importance of identifying and controlling inputs to achieve desired results.
Understanding Y = f(x)
At its core, Y = f(x) signifies that the output (Y) of a process is determined by one or more input variables (x). The function f represents the process or system that transforms inputs into outputs. This equation emphasizes the cause-and-effect relationship inherent in processes, highlighting that variations in inputs can lead to changes in outputs.
Example: In a manufacturing setting, the number of defective products (Y) might be influenced by factors such as machine calibration, operator skill level, and material quality (x).
Applying Y = f(x) in DMAIC
The DMAIC methodology—Define, Measure, Analyze, Improve, Control—is central to Six Sigma projects. Y = f(x) integrates seamlessly into each phase:
Define: Identify the problem and desired outcome (Y).
Measure: Collect data on current processes and inputs (x).
Analyze: Examine data to determine which inputs significantly affect the output.
Improve: Implement changes to optimize critical inputs, enhancing the output.
Control: Monitor the process to ensure sustained improvements.
Example: A call center aims to reduce customer wait times (Y). By analyzing factors like call volume, agent availability, and call handling procedures (x), the center can implement strategies to improve service efficiency.
Real-World Applications
Understanding and applying Y = f(x) has led to significant improvements across various industries:
Manufacturing: Companies have reduced defects by controlling variables such as temperature, pressure, and material consistency.
Healthcare: Hospitals have improved patient outcomes by analyzing factors like staff-to-patient ratios, treatment protocols, and equipment availability.
Finance: Banks have enhanced customer satisfaction by examining transaction processes, service times, and error rates.
Example: A hospital reduced surgical site infections (Y) by standardizing sterilization procedures, staff training, and operating room protocols (x).
Benefits of Using Y = f(x)
Predictability: Understanding input-output relationships allows for more accurate forecasting of process outcomes.
Efficiency: Identifying key inputs helps focus improvement efforts where they will have the most impact.
Quality Improvement: Controlling critical inputs leads to consistent and improved quality of outputs.
Cost Reduction: Optimizing processes reduces waste and operational costs.