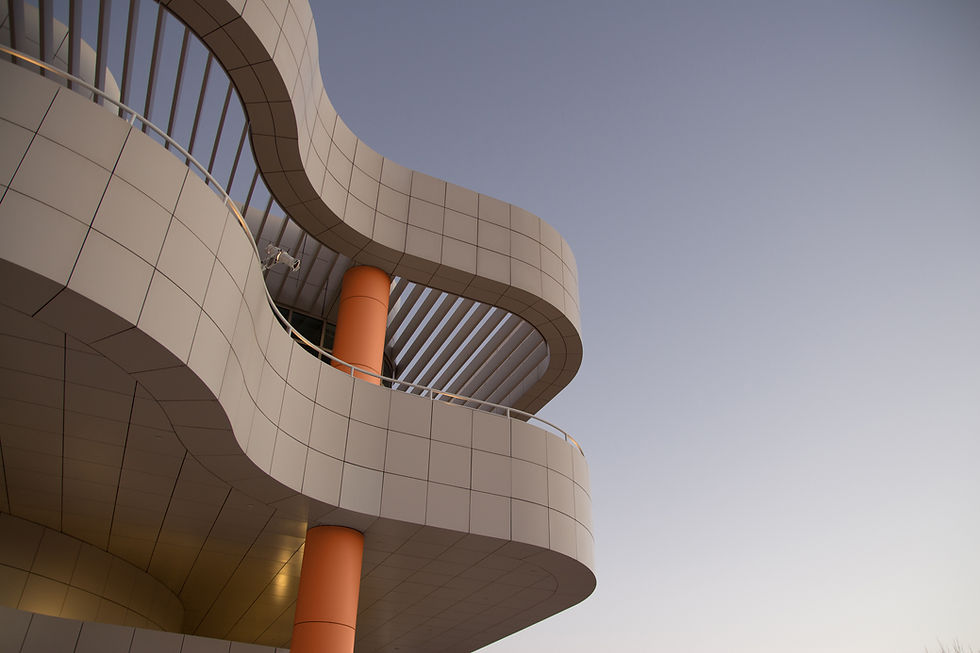
Introduction
Process mapping in Six Sigma is not just about diagrams—it's a strategic method to uncover how work really flows within an organization. By capturing every step, input, and output visually, process maps help teams align operations with customer needs and eliminate inefficiencies. In the Six Sigma framework, these maps are central to identifying improvement opportunities early in a project, especially in the Define and Measure phases of DMAIC.
Whether you're designing a process from scratch or optimizing a legacy system, mapping gives you a high-impact tool to bring clarity, collaboration, and continuous improvement into your workflows.
Why Process Mapping Matters in Six Sigma
Foundation for DMAIC
Process maps play a pivotal role in the Define phase by establishing a common understanding of current workflows. During the Measure phase, these visuals help teams track and quantify process performance accurately.
What It Reveals
A process map can quickly highlight:
Redundant or duplicated tasks
Long cycle times or delays
Decision points that cause confusion
Unclear ownership or handoffs
Impact on Project Outcomes
According to a McKinsey report, companies that leverage process visualization tools improve workflow efficiency by up to 30%. Visualizing a process makes complex operations more understandable and measurable—a cornerstone of data-driven Six Sigma improvement.
Real-World Example
A global logistics company mapped its parcel tracking system and uncovered that over 20% of customer complaints originated from miscommunication during the transfer phase between sorting hubs. Process mapping clarified these gaps, helping them implement role-specific automation that reduced complaints by 47%.
Types of Process Maps Used in Six Sigma
Different projects require different visualization approaches. Here’s a breakdown of the most common types:
1. SIPOC Diagram (Supplier, Input, Process, Output, Customer)
Used in the Define phase to capture a high-level view of the process. It sets boundaries and clarifies upstream and downstream relationships.
2. Basic Flowchart
A step-by-step visual sequence of actions, decisions, and outputs. Ideal for simple processes.
Example: In healthcare, a patient intake flowchart might include steps like registration, insurance verification, and triage.
3. Swimlane Diagram
Illustrates responsibilities across departments. Especially useful in cross-functional projects.
Example: In a bank loan approval process, swimlanes show how different roles (customer service, underwriting, compliance) interact to complete the cycle.
4. Value Stream Map
Goes beyond steps to show time, value-added vs. non-value-added activities, and flow of information. A Lean Six Sigma staple.
Example: A value stream map of an e-commerce fulfillment process might show where packaging delays create bottlenecks.
5. Spaghetti Diagram
Visualizes physical movement in workspaces to reduce motion waste, mostly used in manufacturing and retail.
Pro Tip: Use these tools in combination. Start with a SIPOC to define scope, then use a flowchart or swimlane to dive into task-level details.
Benefits of Process Mapping in Six Sigma
The value of process mapping isn't limited to a beautiful diagram—it drives real results across teams and processes.
1. Improved Clarity and Alignment
Visual workflows reduce miscommunication. Everyone—from frontline workers to executives—gets a unified view.
2. Objective Analysis
Maps expose non-value-added steps, allowing for more accurate root cause analysis and measurement planning in DMAIC.
3. Standardization
Enables the creation of repeatable processes. This is critical in Six Sigma where consistent outputs reduce variation.
4. Enhanced Training and Onboarding
New team members can quickly learn processes via visual guides, reducing ramp-up time and errors.
5. Faster Decision-Making
Executives and stakeholders can make better-informed decisions based on clear process visibility.