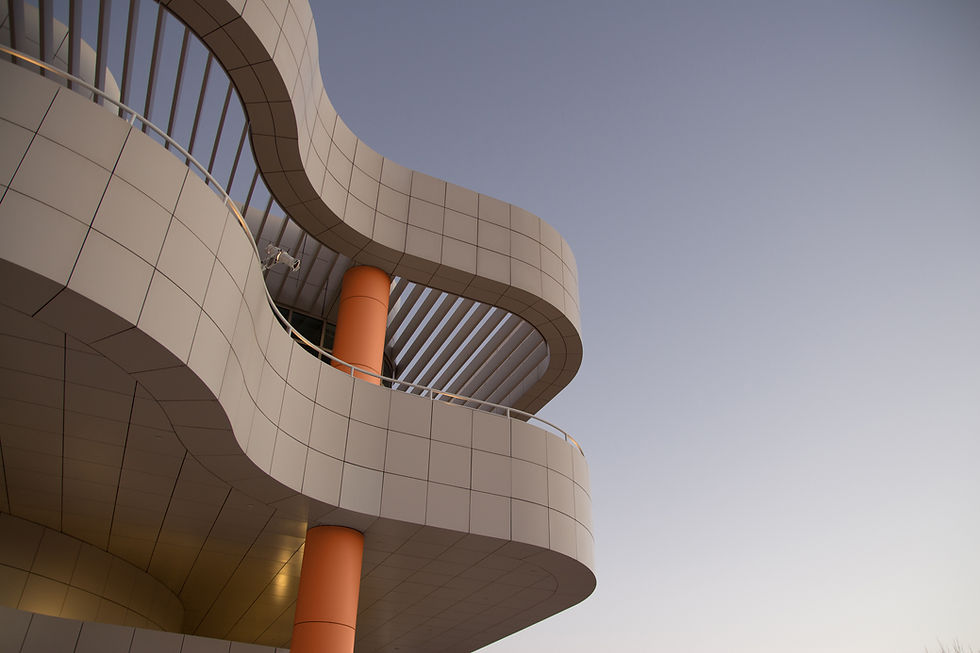
TL;DR
The Fishbone Diagram (Ishikawa Diagram) helps identify root causes of problems systematically.
In Six Sigma, it's used during the Analyze phase of DMAIC.
Key categories typically include People, Process, Equipment, Materials, Environment, and Management.
Real-world application: Reduces guesswork and streamlines process improvements.
It's best paired with data-driven brainstorming and tools like the 5 Whys for maximum impact.
What is a Fishbone Diagram in Six Sigma?
The Fishbone Diagram, also known as the Ishikawa Diagram or Cause-and-Effect Diagram, is a powerful visual tool used in Six Sigma to systematically identify and analyze the root causes of a problem. It's typically applied during the Analyze phase of the DMAIC (Define, Measure, Analyze, Improve, Control) methodology, which is foundational in Six Sigma projects.
Unlike typical brainstorming sessions that can feel chaotic, a Fishbone Diagram provides structure. It forces teams to categorize potential causes into logical groups, reducing the chance of missing critical factors.
The major branches often follow the "6Ms" framework:
Man (People)
Machine (Equipment)
Method (Process)
Material (Inputs)
**Measurement (Data collection)
Mother Nature (Environment)
For instance, a manufacturer facing high defect rates might use a Fishbone Diagram to map issues across these categories. This visualization helps teams spot patterns quickly and prioritize the root causes to address first.
Using visual tools like the Fishbone can increase problem identification efficiency by up to 30%.For more on the broader Six Sigma framework, see our full guide: The Ultimate Guide to Six Sigma: Everything You Need to Know.
How to Create a Fishbone Diagram in a Six Sigma Project
Building a Fishbone Diagram is straightforward, but to be effective, it requires methodical thinking. Here’s how Six Sigma professionals typically approach it:
Step 1: Define the Problem Clearly Place the problem statement at the "head" of the fish. It should be precise and measurable, e.g., "Customer complaints about product delivery delays."
Step 2: Identify Main Categories Use the 6Ms or customize categories to fit the context. In a software project, for instance, categories like "People," "Process," "Technology," and "External Factors" may be more appropriate.
Step 3: Brainstorm Possible Causes For each main category, ask “Why could this be happening?” Encourage diverse thinking without judging ideas initially.
Step 4: Drill Down Further Use techniques like the 5 Whys to dig deeper into each identified cause. This reveals underlying causes, not just symptoms.
Step 5: Analyze and Prioritize Not every cause will have equal impact. Use data and Six Sigma tools like Pareto Charts to prioritize.
Example: A Six Sigma team in a call center used a Fishbone Diagram when facing increased customer churn. Through structured brainstorming, they found issues not just in "Training" (People) but also "Script Errors" (Process) and "Broken CRM Tools" (Equipment).
Real-World Stat: Companies that thoroughly investigate root causes improve operational efficiency by an average of 22%, per a report by McKinsey (source)
Best Practices for Using Fishbone Diagrams in Six Sigma
Even though Fishbone Diagrams are simple in concept, applying them effectively requires attention to best practices:
1. Facilitate, Don’t Dictate The goal is to gather insights from all stakeholders. A neutral facilitator ensures that dominant voices don't overshadow quieter (yet valuable) ones.
2. Keep the Diagram Dynamic Don't treat the Fishbone as "one and done." Revisit and refine it as you gather more data during the Six Sigma project.
3. Combine with Data Validation Fishbone diagrams list potential causes—but not all are actual root causes. Use hypothesis testing or regression analysis where appropriate to validate assumptions.
4. Customize the Categories While the 6Ms are popular, flexibility matters. For instance, in healthcare Six Sigma projects, categories like "Patient Factors" and "Clinical Procedures" might replace some standard labels.
Example: A hospital used a Fishbone Diagram to reduce surgical errors. Their categories included "Team Communication," "Surgical Tools," "Patient Preparation," and "Procedure Protocols," ensuring relevance.
Fishbone Diagram Example in Six Sigma: A Case Study
Problem: Increase in defective electronic components during assembly.
Fishbone Diagram Categories and Key Causes:
People: Inadequate training, frequent turnover
Process: Unclear standard operating procedures
Machine: Equipment maintenance not up to date
Material: Substandard supplier materials
Measurement: Inconsistent calibration of testing equipment
Environment: High humidity affecting assembly line
Using the Fishbone approach, the Six Sigma team identified that "Uncalibrated Testing Equipment" (Measurement) and "Substandard Materials" (Material) were the major culprits. They launched supplier audits and introduced a strict calibration schedule.
Result: Defect rates dropped by 42% within six months.
This real-world case highlights why a Fishbone Diagram remains a timeless, essential tool within Six Sigma projects.
Bonus: Research from Harvard Business Review suggests that structured problem-solving frameworks like Six Sigma can reduce project costs by 20–40% (source).